למי שנדבק בחיידק ההדפסה ב3D (כמוני) ושכואב לו הלב על חומר גלם איכותי גם אם הוא יחסית זול (כמוני), כבר יצא לשאול את עצמו את השאלה הזאת – מה עושים עם שאריות של PLA? חומר ידידותי אמנם, ביופלסטיק שמיוצר מתירס, אך זה לא מצליח לשכנע את הסביבתן שבי שאפשר פשוט לוותר על זה. אז התחלתי להתנסות וזה מה שיצא.
למי שנדבק בחיידק ההדפסה ב3D (כמוני) ושכואב לו הלב על חומר גלם איכותי גם אם הוא יחסית זול (כמוני), כבר יצא לשאול את עצמו את השאלה הזאת – מה עושים עם שאריות של PLA? חומר ידידותי אמנם, ביופלסטיק שמיוצר מתירס, אך זה לא מצליח לשכנע את הסביבתן שבי שאפשר פשוט לוותר על זה. אז התחלתי להתנסות וזה מה שיצא.
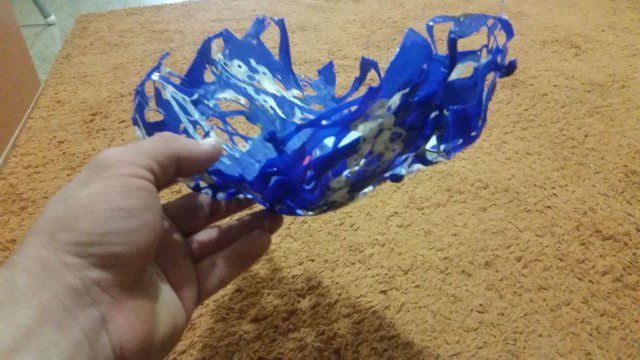
ניסיון ראשון ראשון - המסה על אבן
אז מה בעצם הקטע?
טכנולוגיית ההדפסה הנפוצה ביותר ב3D, שנקראת Fused Deposition Modeling, עושה בדיוק את זה – התכה של חומרים תרמופלסטיים, זאת אומרת, חומרים פלסטיים שתוכננו כך שיהיה אפשר לעבד אותם באמצעות חום.
PLA, או בעברית, חומצה פולילקטית, הוא ביופלסטיק שמיוצר מעמילן של תירס, קנה סוכר או גידולי עמילן אחרים. ה-PLA הוא תרמופלסטי במובן שהוא מותך למצב צבירה צמיגי בטמפרטורה של בין 190 ל-230 מעלות צלזסיוס, וכשהוא מתקרר וחוזר למצב צבירה מוצק הוא לא מאבד כמעט מתכונותיו הראשוניות. הPLA הוא הפלסטיק הנפוץ ביותר בתעשיית ההדפסה ה3D החובבנית, ולמרות שאני לא יודע למה בדיוק, אני שמח שלפחות המקור הוא מקור מתחדש.
עד כאן הרקע.
להדפסה תלת מימדית, על אף הדעה הרווחת בקהילת הייצור, יש פחת. בעיקר כשהיא עובדת במרחבים ציבוריים כמו סדנאות קהילתיות, אוניברסיטאות ובתי ספר. בפחת, כוונתי לחומר גלם שאינו מגיע להיות חלק מהתוצר הסופי (כמו שקליפה של קולורבי היא פחת של הקולורבי כמוצר מזון). איפה הפחת הזה נוצר? בכמה נקודות, מהיותר נפוצות לפחות:
- תמיכות לחלקים – כדי להדפיס את האיש כאן למטה, היה נחוץ להחזיק חלק מההדפסה באוויר (למשל את הידיים המשולבות), ומכיוון שזה לא אפשרי פיסיקלית, חומר תמיכה צריך להבנות מלמטה מתחת כל חלק בעל שיפוע שלילי שהמדפסת לא יכולה להתמודד איתו. כל התמיכות הן חומר שלא משתתף בתוצר הסופי.
- הדפסות מהירות – במקום להדפיס הדפסה ארוכה כדי לבחון האם רעיון מסוים עובד, או האם המארז נסגר על החומרה שלכם, אתם מדפיסים את הקופסא בdraft, הדפסה מהירה ומגורענת אבל כזו שתאפשר לכם לא להדפיס את הכל באיכות טובה רק כדי לגלות שזה לא מתאים. אז אתם מדפיסים רק חלק מהמודל, או מדפיסים אותו באיכות נמוכה, אבל בסוף הוא מוצא את עצמו באותו סל כמו התמיכות מסעיף 1.
- הדפסות שנשברו – הדפסתם חלק, וחצי שעה אחרי שהכנסתם אותו לעבודה מאומצת, גיליתם שהוא נסדק ושהייתם צריכים להדפיס אותו עם עובי דופן עבה יותר. ההדפסה הזאת – הולכת לסל.
בקיצור, הבנתם את העניין. יש הרבה פחת. אז מה עושים?
יש טכנולוגיות מקומיות למחזור החומר, אבל להחזיר את החומר למדפסת זה יותר מסובך ממה שזה נשמע. אפשר גם לזרוק לקומפוסט וכאילו להשתיק את המצפון, אבל החלטתי שזה לא מספק אותי.
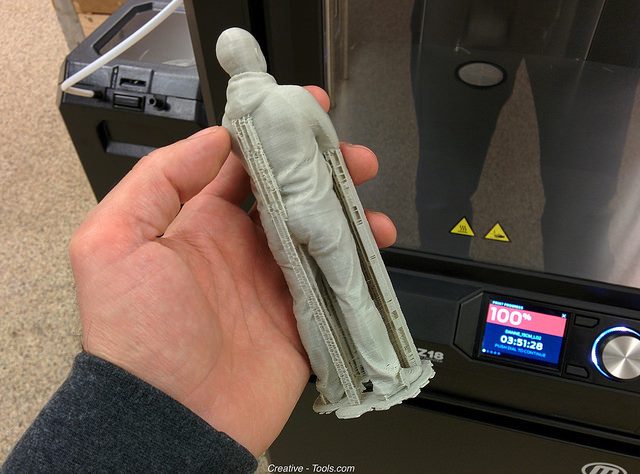
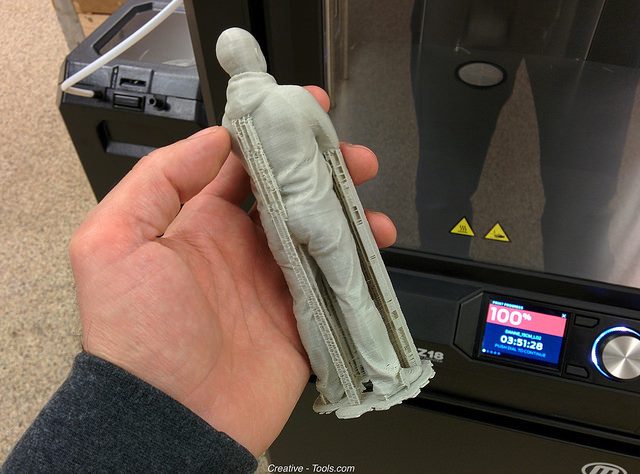
איש עם הרבה תמיכות
המסה בתנור
כמו שציינתי, הPLA נמס בטמפרטורות שתנור ביתי מגיע אליהם בקלות. מה שגרם לי לחשוב על השיטה הזאת, שאני בטוח שאני לא פיתחתי אותה באופן בלעדי, היה שילוב של שלושה גילויים: האחד, מדריך של חן אופיר העונה לשם “להכין קערה מתקליט” שבו היא המיסה תקליטים ישנים בתנור ועשתה מהם דברים יפים; השני, פריצה של טכנולוגיה שנקראת Vaccum Forming כמערכת יצור שולחנית בדומה למדפסת 3D. עד עתה השיטה הזאת הייתה מוגבלת לנפחים גדולים, משטחים גדולים ומכונות גדולות, עד שהגיעה חברה קטנה בקיקסטארטר ועשתה מהטכנולוגיה הזאת משהו שאפשר לשים על השולחן במשרד. השלישי, חרוזי גיהוץ – כן, משחק ילדים שראיתי פעם ראשונה אצל חבר של בני, שבו בעזרת מגהץ לוחצים על חרוזי פלסטיק ומלחימים אותם אחד לשני.
השלב הראשון היה לקחת שאריות ולסדר אותן על מגש אפייה עם נייר אפיה כדי שיכסו את המקסימום האפשרי. ניסיתי לדאוג שלא יהיו חורים, אבל עד עתה בכל הניסיונות שלי לא הצלחתי (ראו שלב הבא). זמן ההמסה תלוי בכמות הפלסטיק שהכנסתם למגש, ולצורך זה לא הייתי עולה על 200 מעלות בהמסה כדי לא לשרוף החלקים העליונים.
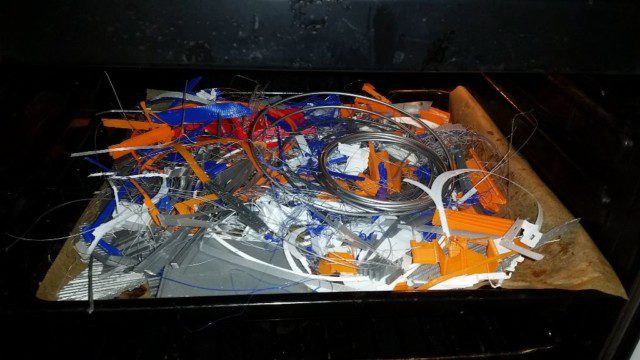
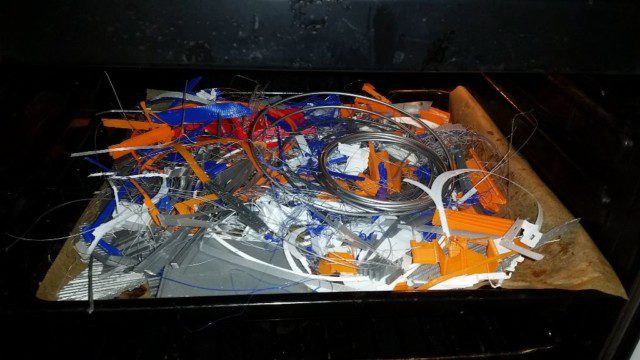
בלאגן של שאריות על מגש תנור האפיה
(ניסיון ל)תיקון חורים
קשה לדעת איך בדיוק הכל ייראה כשכל הפלסטיק יימס לשכבה פחות או יותר אחידה במגש, אבל תצפו לחורים. אם אתם מנסים לייצר משהו שצריך להיות אטום, וזה אפשרי לדעתי, דאגו להוסיף חתיכות פלסטיק על החורים ולהחזיר את המגש לתנור עד שהן נמסות גם. אם תחזרו על התהליך כמה פעמים, אפשר יהיה למלא את כל החורים.
כשכל החורים מתמלאים נותנים לפלסטיק להתקרר עד הסוף ומפרידים את נייר האפייה.
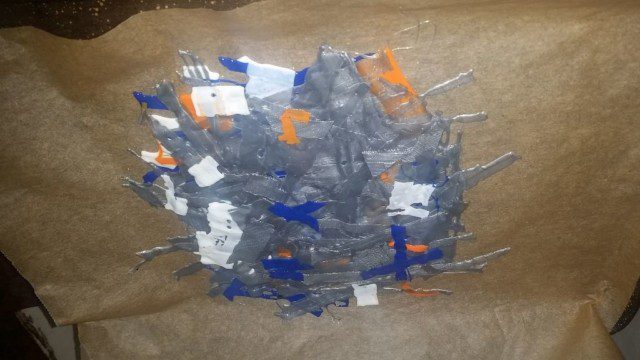
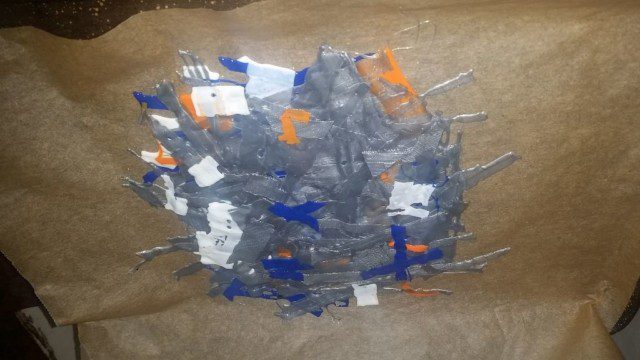
משטח אחר - חוזר לתנור עם התיקונים הכחולים אחרי סבב אחד
בחירת האובייקט אותו נרצה להעתיק והחזרה לתנור
חשוב לומר שזה לא בדיוק העתקה כמו בייצור בוואקום. מה שנוצר בסוף הוא סוג של רמז למודל אותו ניסינו להעתיק, משהו כמו יצירת אומנות בהשראת המודל הראשוני.
אז אנו מניחים את המודל בתנור ועליו את משטח הפלסטיק ונותנים לכוח המשיכה לעשות את שלו (מכאן השם Gravity Forming).
אני עשיתי ניסויים עם שלושה מודלים עד כה – חלוק נחל, קערת זכוכית וקערת מתכת. הרי הם לפי סדר ההופעה למטה.
עכשיו אספר לכם על כל אחד מהניסויים בצורה מפורטת יותר.
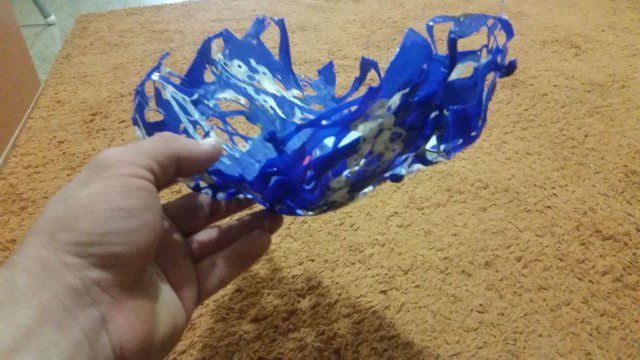
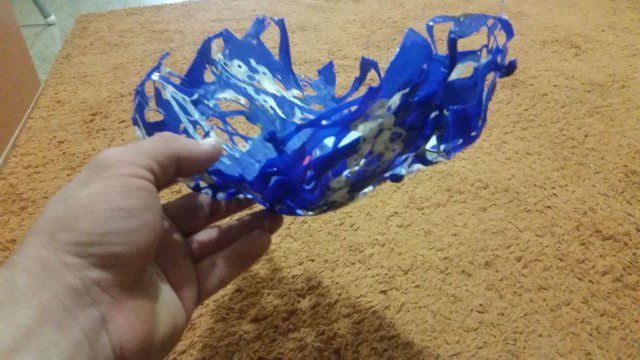
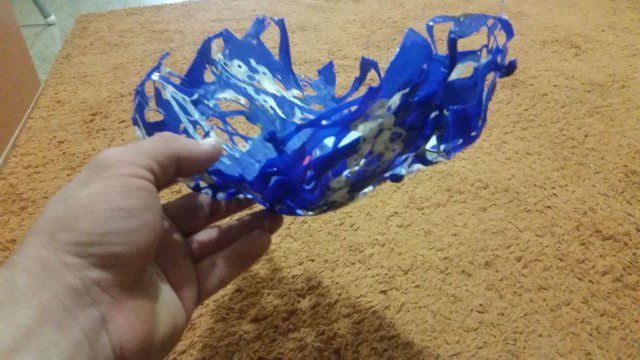
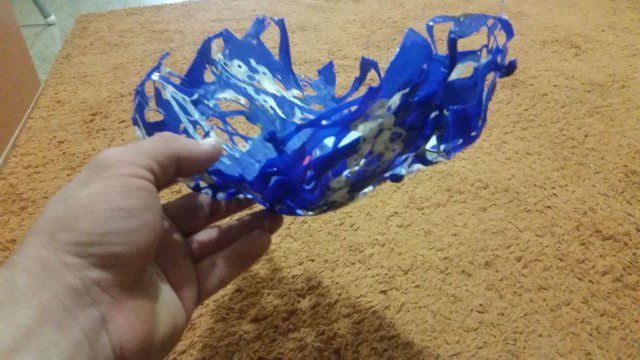
ניסיון ראשון ראשון - המסה על אבן
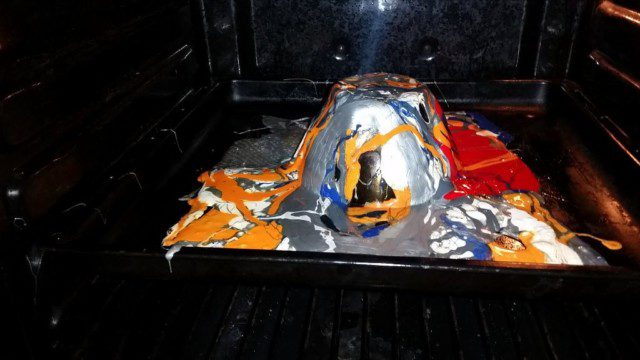
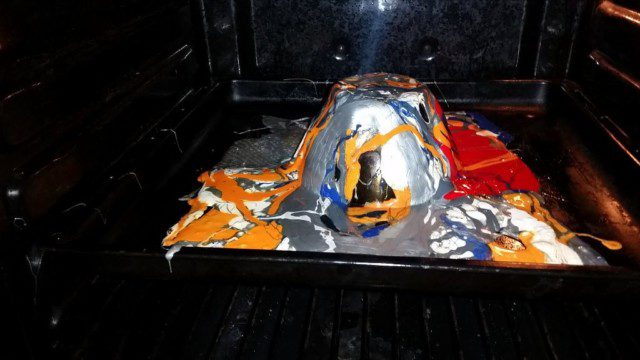
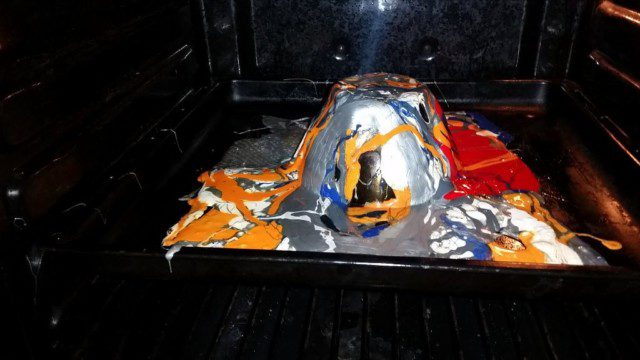
המסה על קערת זכוכית
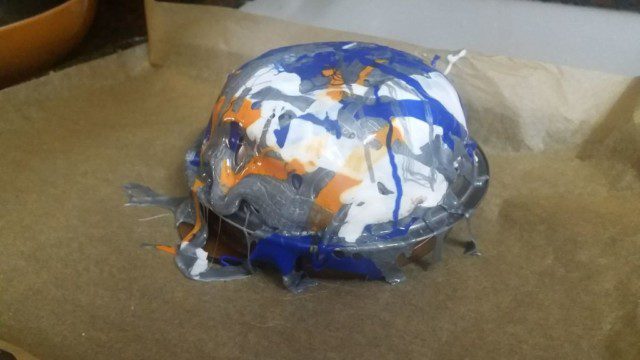
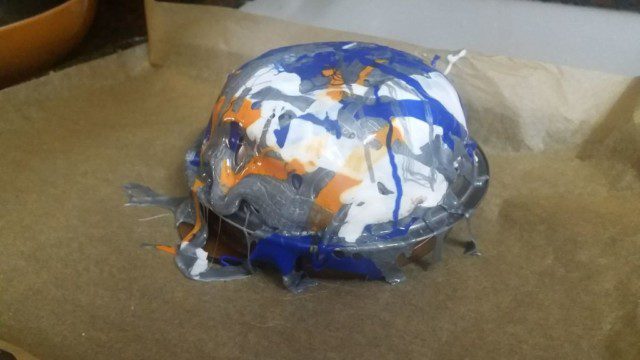
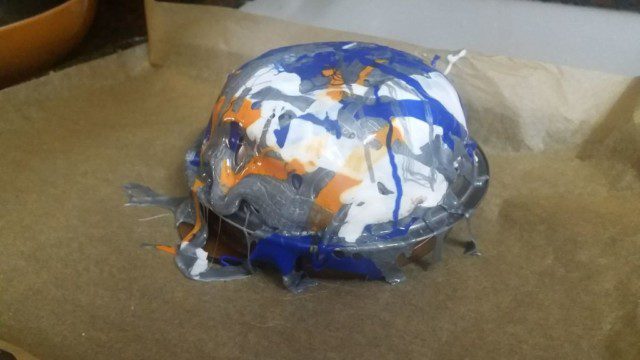
המסה על קערת מתכת
המסה על אבן
יש לי רק תמונה אחת מהניסיון הראשון הזה, וגם רק מסקנה אחת. המסה התרמית של האבן גורמת לכל התהליך להיות איטי מאוד, גם הקירור וגם החימום. מציע לוותר על הניסיון מראש. זה לא פרקטי, אלא אם כן יש לכם מודל מאוד ספציפי שעשוי מאבן, שיש, שנהב או משהו כזה, ואתם רוצים להעתיק אותו. אבל עדיף להמנע מזה.
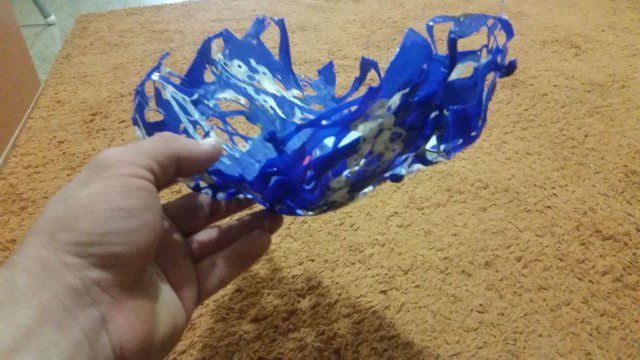
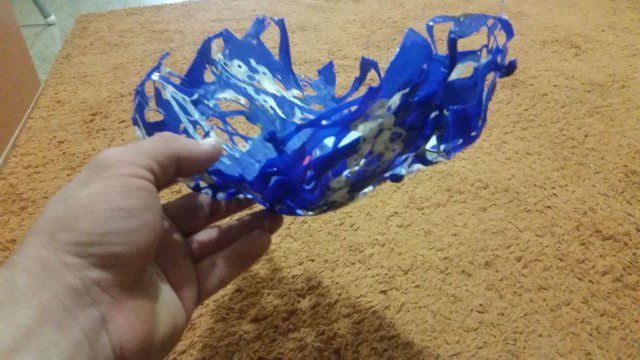
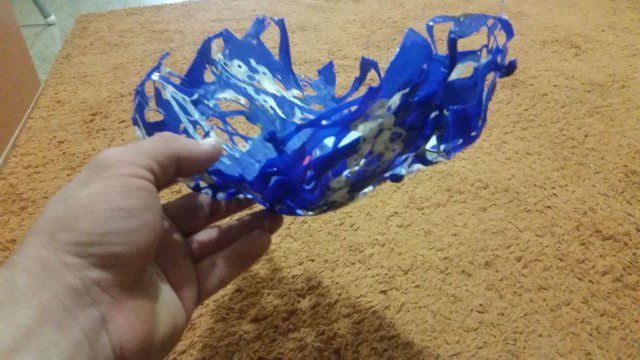
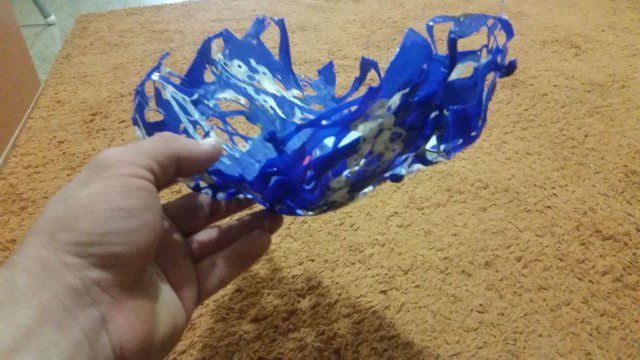
ניסיון ראשון ראשון - המסה על אבן
על זכוכית
לשלב הזה כבר הגעתי מוכן עם הרבה פלסטיק כדי לייצר שכבה רצינית. טעות אחת הייתה שהכנתי מגש שלם בשביל קערה די קטנה. המסקנה היא שאם אתם יודעים מראש על מה תרצו לעשות Gravity Forming תדאגו שחומר הגלם יתאים לגודל שלו (ראו את הניסיון השלישי עם קערת המתכת).
דבר נוסף – למרבה הפלא, הפלסטיק נדבק די טוב לזכוכית. כעת אני עומל על להוציא אותו משם, אבל הניסיון הזה אומר לי שכדאי להמנע מתבניות זכוכית לתהליך הזה. אם כבר החלטתם לעשות זאת, דאגו לציפוי בשמן, בנייר אפיה או משהו אחר. אפשרות נוספת היא להוציא מהתנור לפני קירור סופי וכשהפלסיק עוד קצת גמיש, לעקם את הדפנות ולנסות לשלוף את הקערה החוצה.
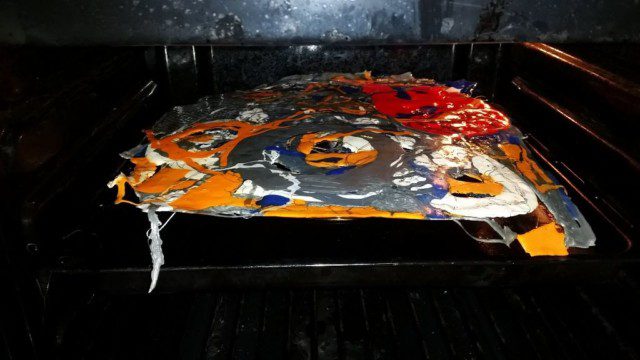
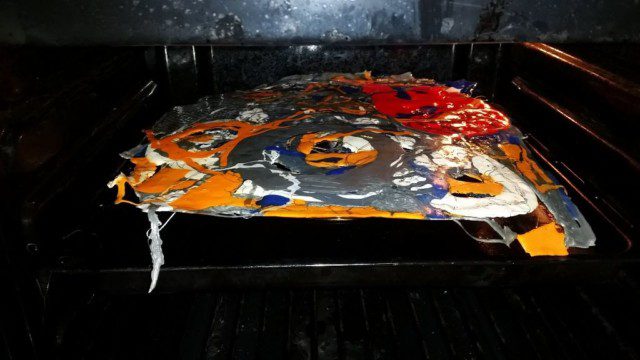
תבנית שלמה בהמסה
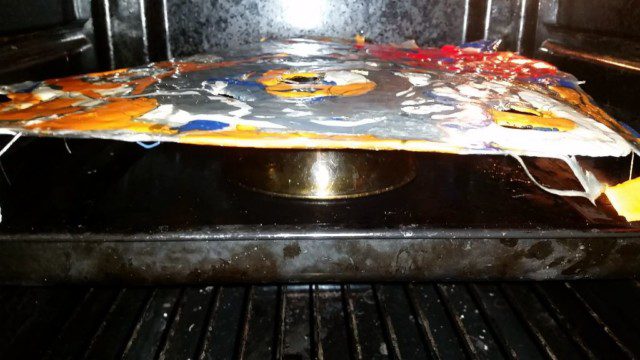
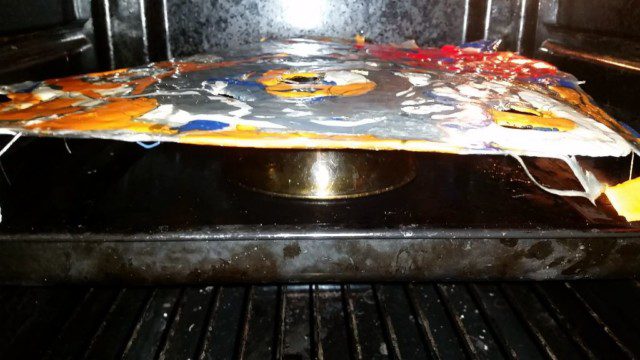
אחרי התקררות של המשטח, עם קערת הזכוכית מתחת
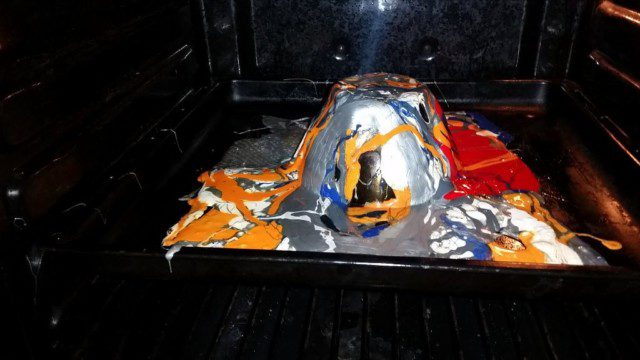
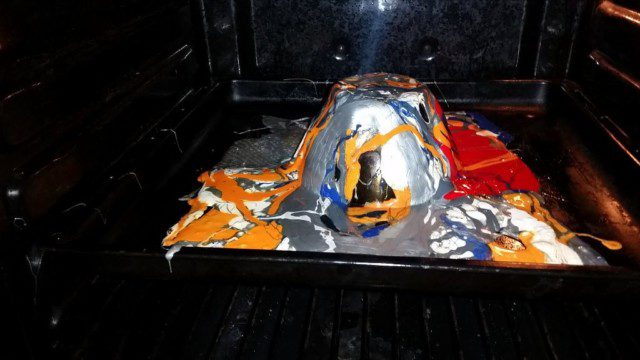
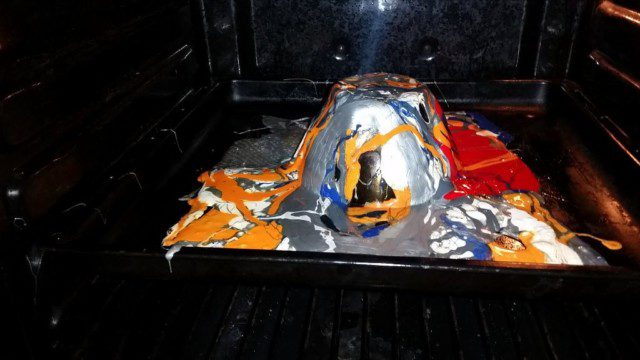
המסה על קערת זכוכית
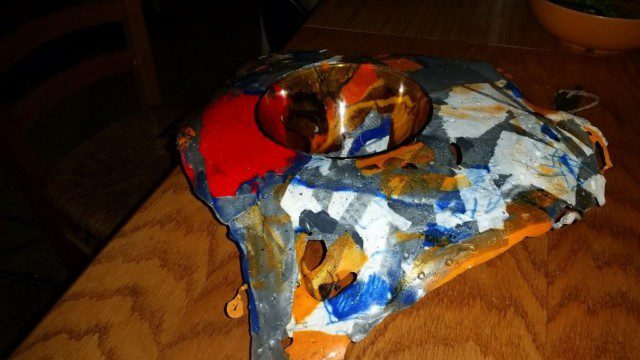
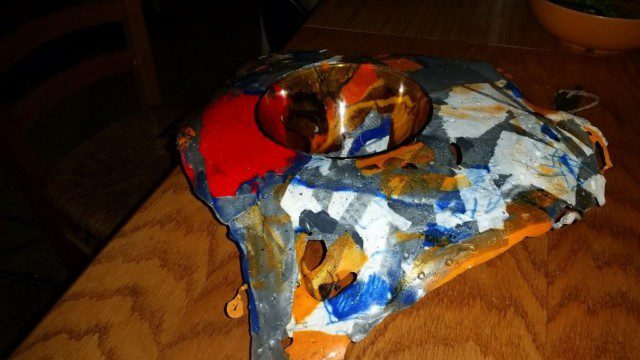
הקערה הקבורה בתוך הפלסטיק
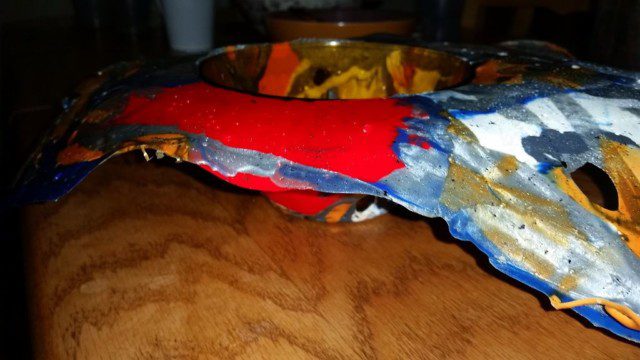
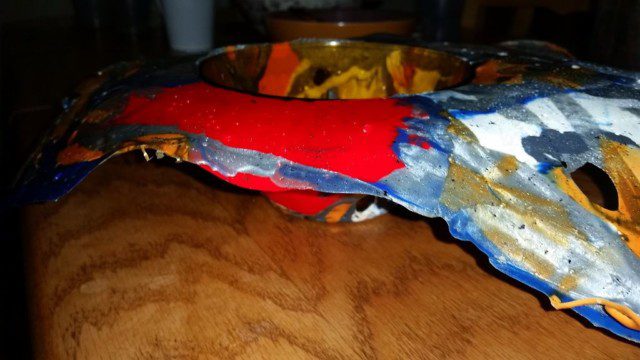
ומבט מקרוב
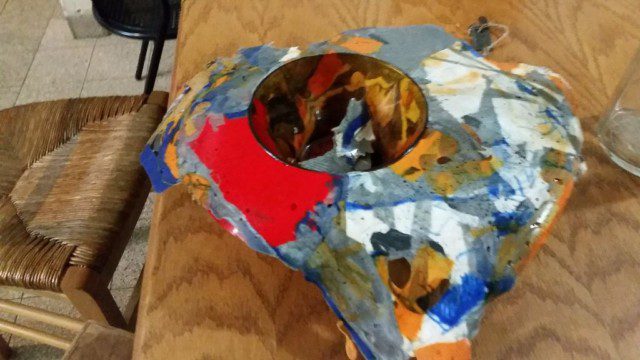
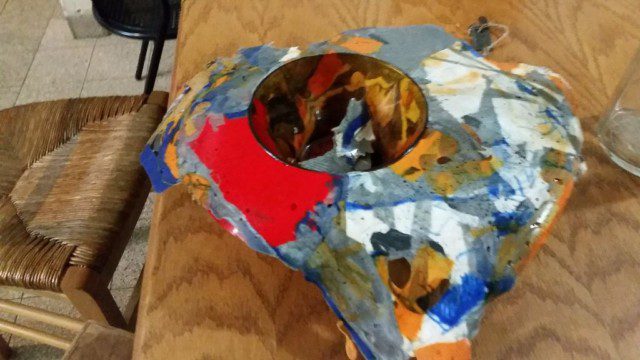
ומבט ממעל
על נירוסטה
אולי לא על כל מתכת זה יצליח בצורה דומה, אבל עם הנירוסטה קצרנו הצלחה. ראשית, למדתי מהניסיון על הזכוכית והכנתי מראש משטח קטן יותר שהיה גדול רק בקצת מההיטל של הקערה. שנית, נראה שהמתכת מגיבה טוב יותר לפלסטיק, והיה יחסית קל לנתק את הקערה מהמודל.
לאחר שהקערה יצאה בפעם הראשונה, ועוד לפני שהפרדנו את הנירוסטה מהפלסטיק, החלטתי לעשות עוד סיבוב עם אלמנט יותר מחושב מבחינה עיצובית – ספירלה כתומה על כל הבלאגן הרנדומלי שהיה לפני. ובכן, רצונות לחוד ומציאות לחוד – הספירלה התעוותה לפני שהומסה, כנראה כי החום שובר את הכיפוף שעשיתי ומחזיר אותו קרוב לצורתו המקורית, מה שנקרא זיכרון מולקולרי (אולי?)
וכאמור – את קערת הנירוסטה יותר קל להפריד.
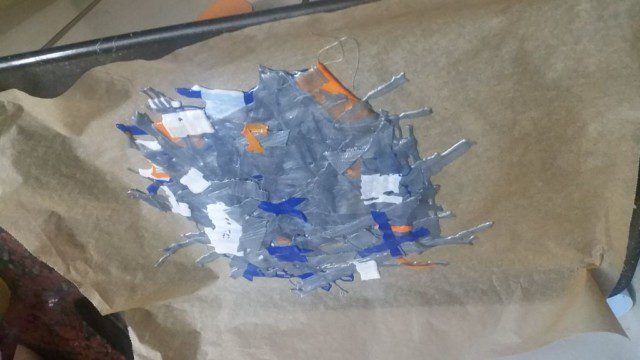
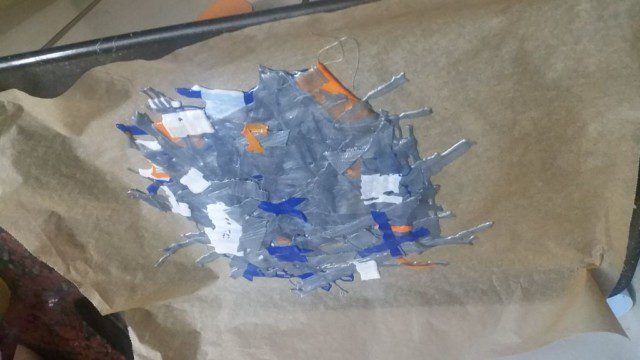
המשטח לקערת הנירוסטה
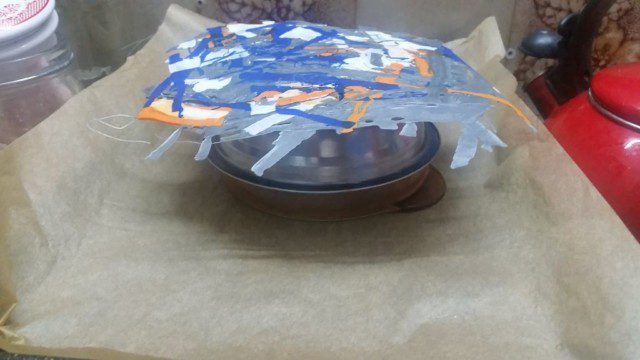
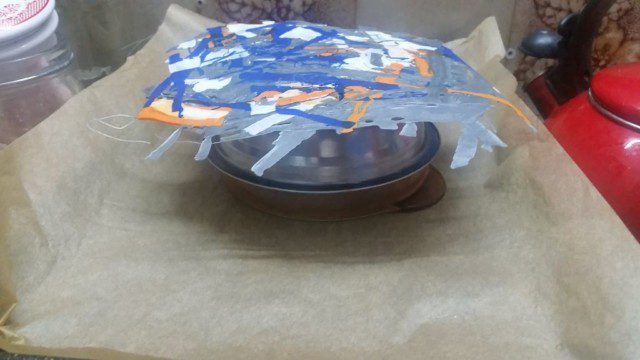
הנחת המשטח על הקערה (הרמתי אותה מהמגש עם עוד קערה אחרת שלא השתתפה באמת בניסוי)
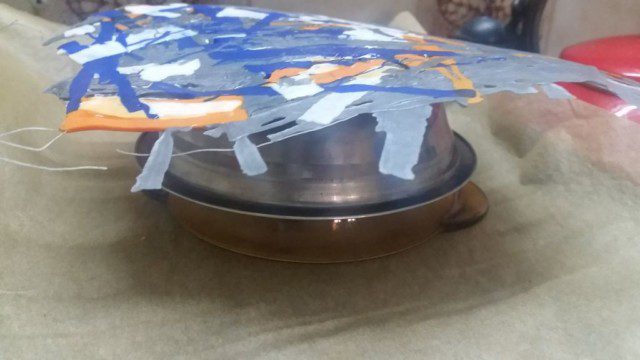
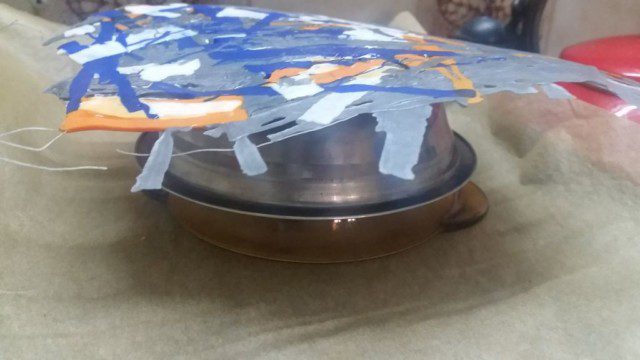
וקצת מקרוב יותר
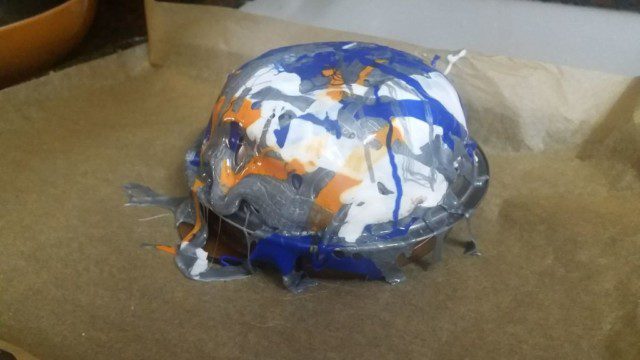
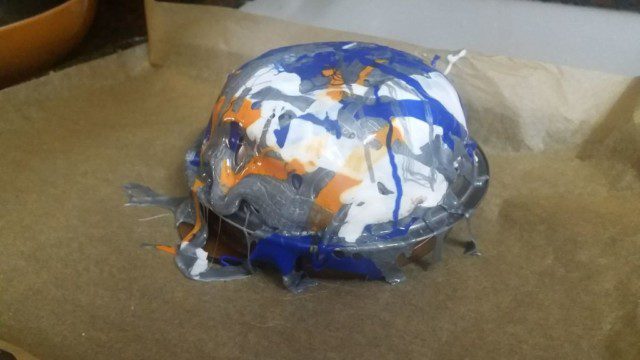
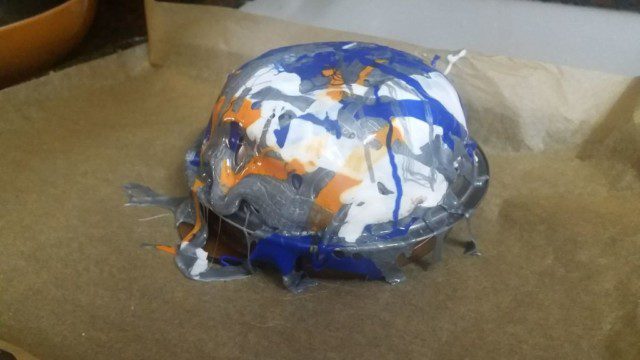
המסה על קערת מתכת
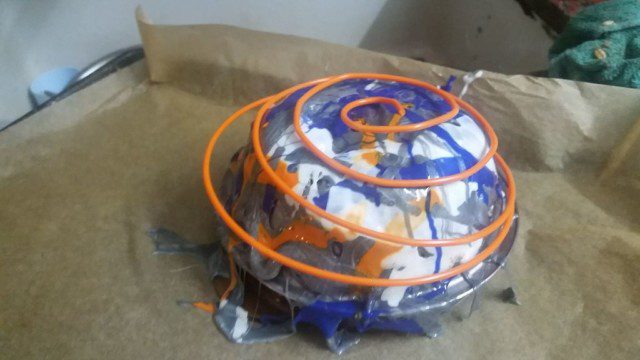
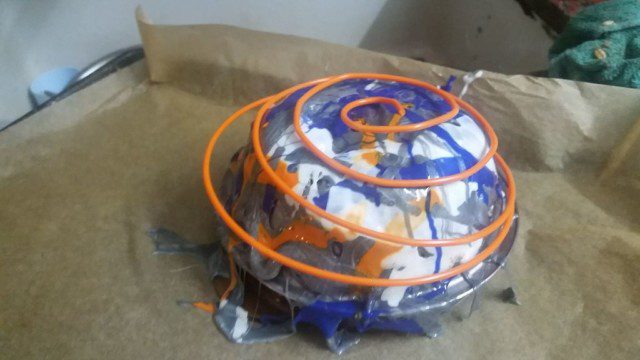
החלטתי לנסות להוסיף אלמנט יותר מחושב - ספירלה כתומה
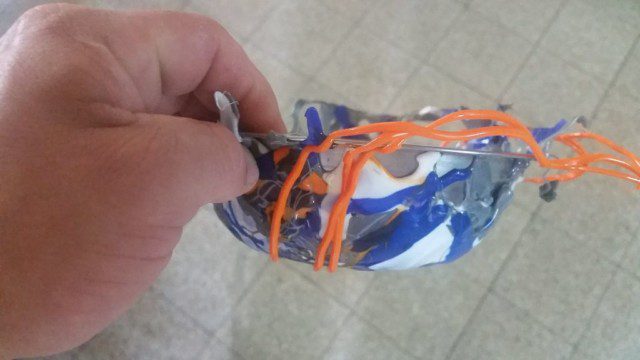
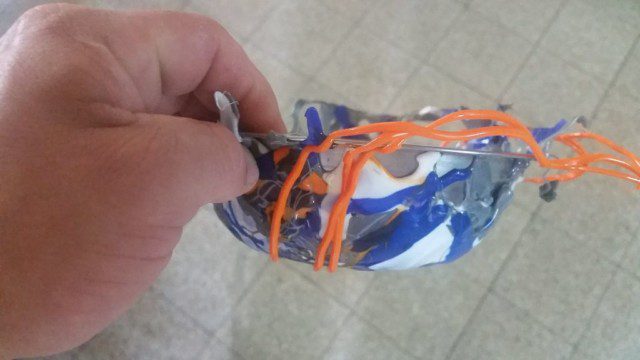
וזה מה שיצא מהספירלה
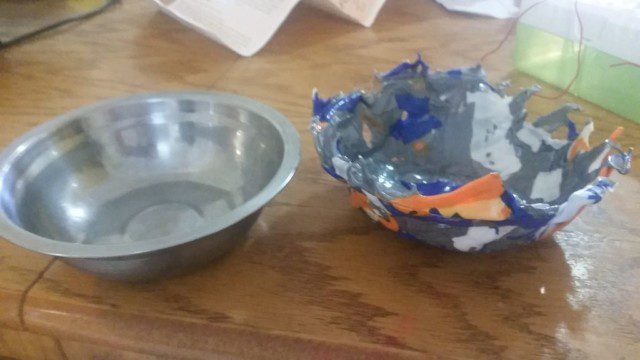
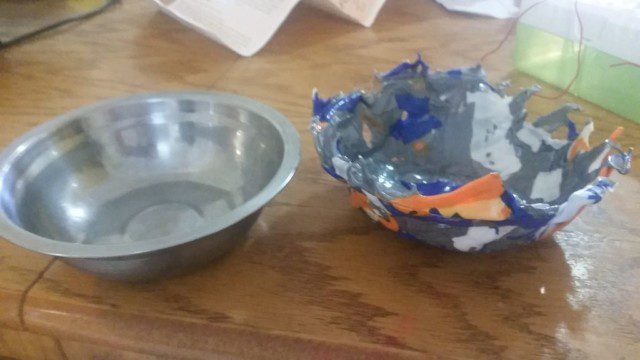
הקערות אחרי ההפרדה
מה הלאה
השלב הבא יהיה לנסות לייצר דרך להכין חומר גלם אטום בשכבה אחידה (כנראה מסגרת מתכת שתתן את הצורה או משהו כזה) וגם – הכנתי משטח נוסף של מגש שלם ואנסה לראות מה יוצא כשאני מנסה לחתוך את החומר בלייזר. אולי נעלה על משהו חדש. אז יאללה – עופו על Gravity Forming
אם יש לכם מה להוסיף – מוזמנים בתגובות.
לתוכן זה נכתבו 0 תגובות